Our Services
At Mahalaxmi Enterprises, we offer a wide array of services designed to meet the diverse needs of our clients, including:
Die Casting Services
Precision die casting for various industrial applications ensuring quality and durability.
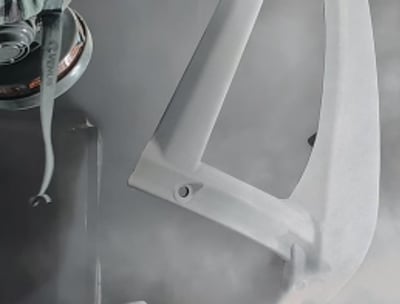
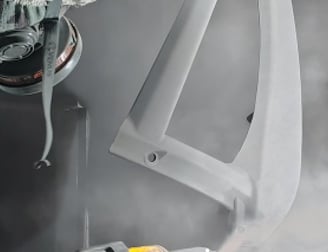
CNC Machining
We specialize in precision CNC machining, offering high-quality components tailored to your specifications.
Our powder coating solutions ensure a durable and attractive finish for a wide range of products.
Powder Coating
VMC Operations
Our Vertical Machining Center (VMC) services provide accuracy and efficiency in manufacturing processes.
Current Infrastructure
At Mahalaxmi Enterprises, our infrastructure is designed to support a seamless and efficient production process. We continuously invest in advanced machinery, automation, and technology to ensure we deliver high-quality products and services. Below is a detailed breakdown of our current infrastructure:
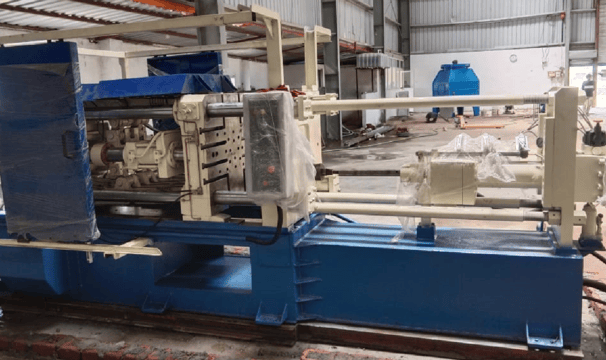
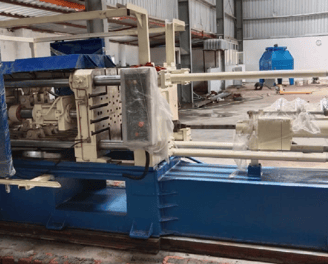
1. High-Pressure Die Casting (HPDC) Plant
Our High-Pressure Die Casting (HPDC) facility is equipped with state-of-the-art technology, designed to meet the highest standards of precision and quality in aluminum casting.
Machines:
180 Ton RM Techno Manual Machine – Ideal for small to medium-sized components, ensuring reliable production.
300 Ton Yuzumi Automatic Machine – Automated for higher efficiency and consistency in output.
Furnaces:
Electric Holding Furnace for each machine, ensuring precise temperature control and consistent material quality.
Production Capacity:
Melting Capacity per Day: 4 Tons
Monthly Production Capacity: 120 Tons
Current Load: 10 Tons
Spare Capacity: 110 Tons
Facility Size:
7,500 sq. ft. with room to expand and accommodate up to four more die casting machines of varying tonnages as required by future demand.
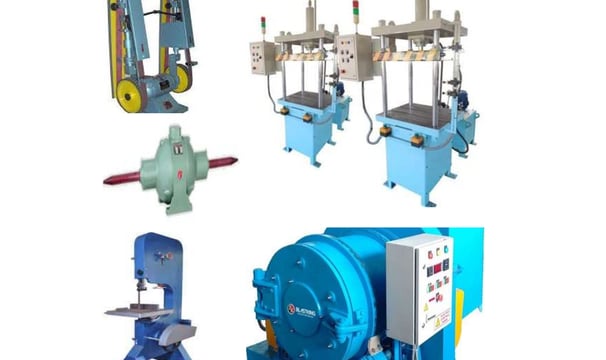
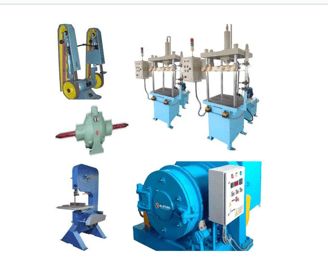
2. Post-Processing Operations
Our Post-Processing Unit is fully equipped to handle all post-casting operations, ensuring the highest levels of precision, quality, and productivity without relying heavily on human intervention. Key features include:
Hydraulic Trimming Press – 2 units for high-precision trimming and removal of excess material from castings.
Band Saw and Sanding Machines – 2 units equipped with belt grits ranging from 80 to 220 to ensure smooth finishes.
Shot Blasting Machine – 1 unit for removing surface impurities and enhancing the finish of cast components.
Buffing Machines – 2 units designed to provide a matte finish to cast parts, ensuring consistent and aesthetic results.
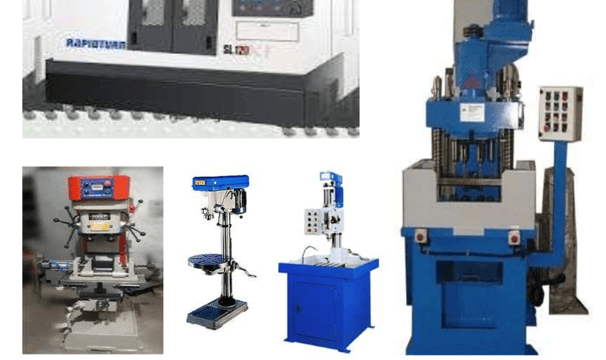
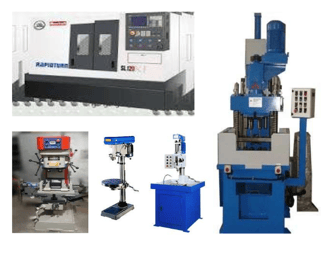
3. Machining and CNC Operations
We maintain full control over the machining processes by utilizing automated machining cycles and special-purpose machines (SPMs), ensuring no human intervention during the machining process. Our CNC and VMC operations are outsourced but tightly monitored for quality.
Machinery:
SPMs (Special Purpose Machines) – 2 units designed for specific machining operations.
Multi-Head Drilling & Tapping Machine – 1 unit for simultaneous drilling and tapping operations.
Drilling and Tapping Machines – Multiple units for various part sizes and requirements.
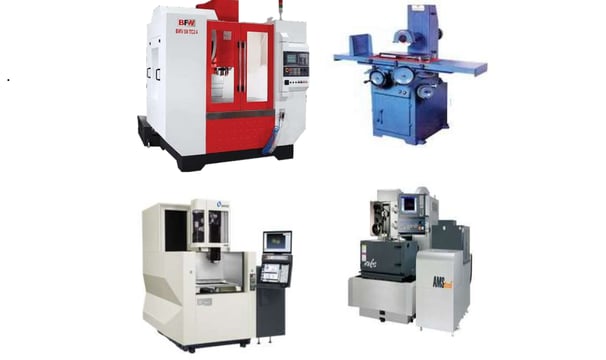
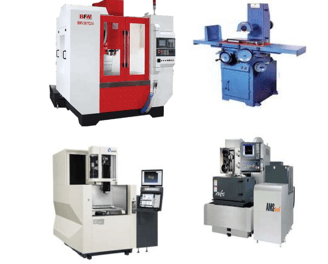
4. Tool Room
We have an outsourced Tool Room dedicated to manufacturing high-quality tools and tool spares. This ensures the longevity of tools, minimizes downtime, and maintains the highest standards in production.
Key Equipment:
VMC (Vertical Machining Center)
EDM (Electrical Discharge Machine)
Wire Cut Machine
M1TR Milling Machine
Cylindrical Grinder
Milling Machine
Tool and Cutter Grinder
Software Capabilities:
Design Software for accurate tool design and modifications.
Simulation Capability to test designs and processes before physical implementation.
Additional Capabilities:
Heat Treatment facilities to enhance tool durability and performance.
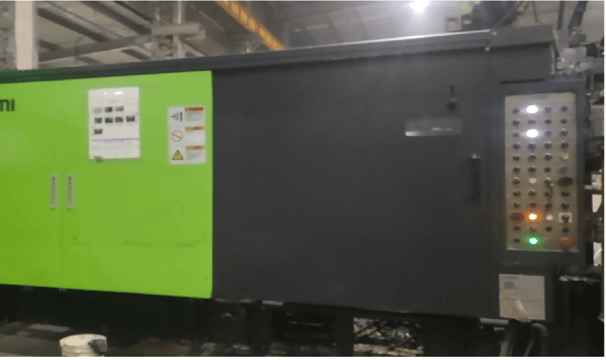
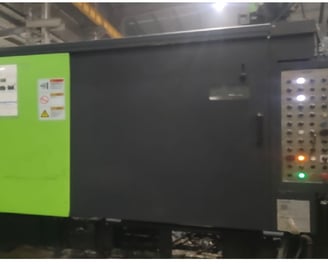
5. Foundry Specifications
Our foundry specializes in Pressure Die Casting, optimized for small to medium-weight aluminum components.
Furnace Size:
150 kg and 300 kg capacity electric furnaces.
Part Weight Range:
Components ranging from 0.045 kg to 2.0 kg in weight.
Quality Assurance & Testing Facilities
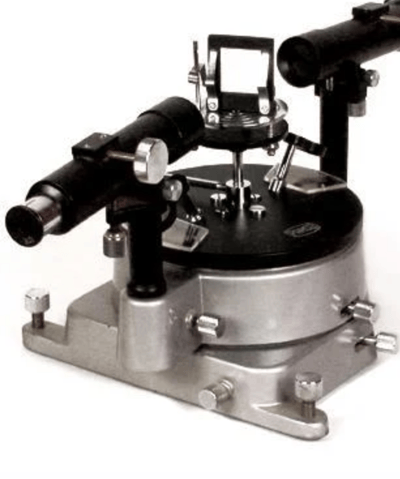
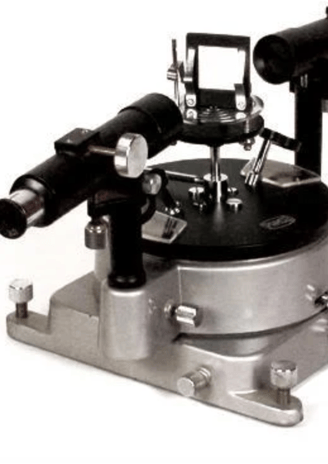
Spectrometer
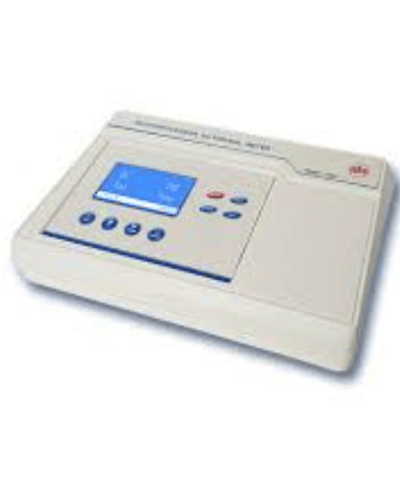
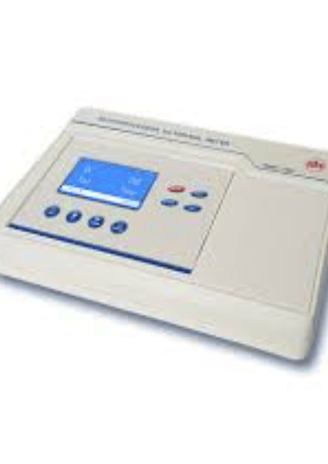

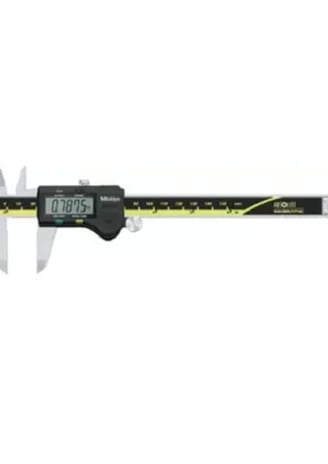
Conductivity Meter
Digital Vernier (0-300 mm)
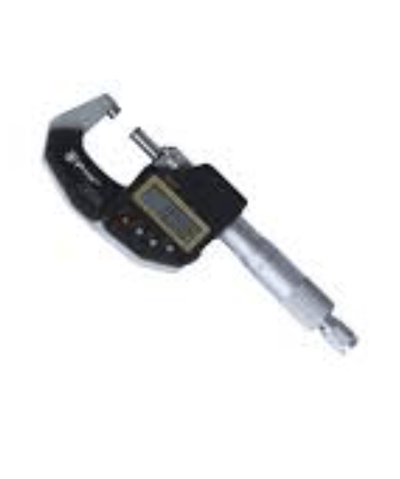
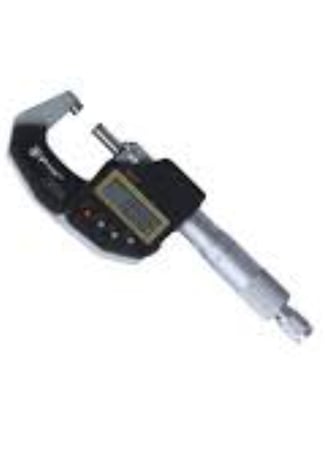
Digital Micrometer
(0-25 mm)
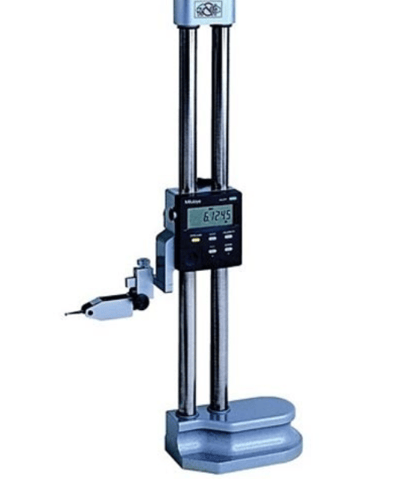
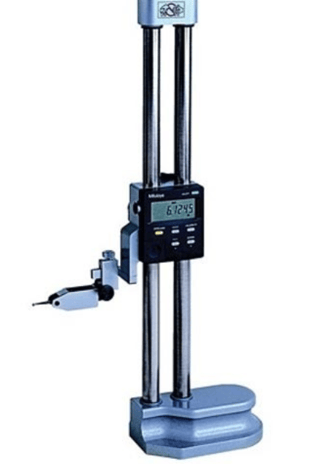
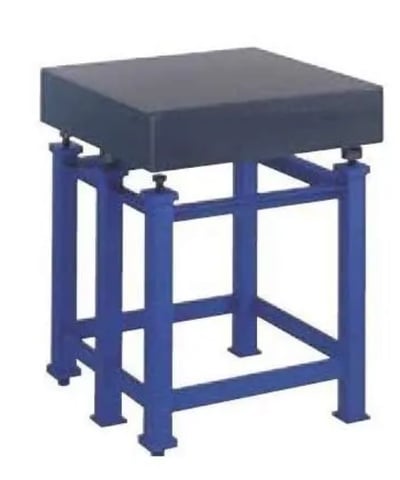
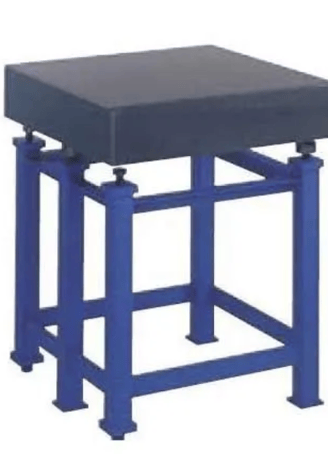
Digital Height Gauge
(0-300 mm)
Surface Plate
Mahalaxmi Enterprises
Your Trusted Partner In Aluminium Die Casting Parts Manufacturing
vishalpatare@mahalaxmienterprises.info
+91 8076753915
© 2024. All rights reserved.